독일 스마트 팩토리의 주목할 만한 사례들
슈투트가르트 근교의 진델핑엔 메르세데스-벤츠 공장에서는 S클래스·E클래스·마이바흐를 생산한다. 생산의 80%를 로봇이 맡고 로봇이 하기 힘든 세부적인 업무를 사람이 작업하는 시스템으로 가동되고 있다. 메르세데스-벤츠는 2020년 9월 가동을 목표로 진델핑엔 공장에 100% 디지털화한 차세대 공장 ‘팩토리 56’을 추진 중이다.
팩토리 56은 축구장 30개 크기에 해당하는 22만㎡ 면적에 트럭과 전기자동차, 새로운 S클래스 모델(223 시리즈), EQS 모델을 생산한다. 전 세계 자동차 공장 최초로 5G 네트워크가 도입됐고 인공지능(AI)과 각종 스마트 디바이스가 적용된다.
‘팩토리 56’도 완전한 자동화 공장이 아니라는 점에서 앞서 언급한 프로덕션 레벨4의 기준에 부합한다. 즉, 작업을 조직하고 배송하고 품질을 보증하는 모든 과정에서 인간과 기계가 협력하는 구조이며 이를 디지털화하는 것을 목표로 한다. 이를 통해 기존 생산 체계에서 발생할 수 있는 오류나 비효율적 상황을 최소화하고 직원 간 원활한 소통을 도모하며 친환경적이고 높은 연료 효율성을 달성해 공장의 능률을 높이는 것이 주된 목적이다.
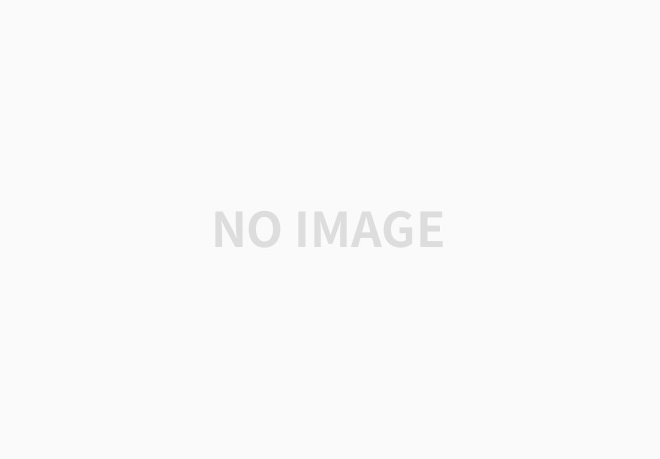
또한 공급 업체·개발·설계·생산에서 고객에게 배송되기 위한 물류센터 이동까지 전체 가치 사슬을 망라하는 360도 네트워킹을 목표로 하고 있다. 이는 무인 운송 시스템(FTS), 무선 인식(RFID), 5세대 이동통신(5G) 기술의 합작품이다. 고객은 메르세데스-벤츠 애플리케이션(앱)에서 차량 생산 과정을 직접 확인할 수 있다.
또 다른 측면에서의 ‘영리함’은 공장이 태양광 발전 시스템 등 재생에너지를 통해 전기를 생산한다는 점이다. 이를 통해 매년 5000MWh의 전기가 절약된다. 메르세테스-벤츠는 2022년까지 모든 공장을 이산화탄소(CO₂) 중립으로 운영할 계획이다.
이 밖에 독일 인더스트리 4.0의 선두 업체인 보쉬의 사례도 주목할 만하다. 특히 최근 개발한 넥시드는 제조·물류의 전 과정에서 전체적인 가치 흐름에 필요한 소프트웨어와 서비스를 집약한 것이다. 보쉬는 전 세계 270개 이상의 공장에서 체계적으로 관련 지식을 심도 있게 습득해 이를 소프트웨어 솔루션으로 바꿨다. 이를 통해 노동자가 쉽고 빠르게 의사 결정을 내릴 수 있도록 지원함으로써 생산 과정을 지속적으로 개선해 나간다. 이를 통해 기계 능력은 기존 대비 15%, 생산 능력은 5~10%로 향상할 수 있다.
노동자들은 앱을 참조해 기계의 상태 보고서를 얻을 수 있고 유지·보수 작업 또는 자재 공급과 같은 작업을 명확하고 쉽게 얻을 수 있다. 또한 모든 작업 과정이 디지털 문서와 이미지·비디오의 형태로 쉽게 저장되고 누구나 접근할 수 있기 때문에 고장 시 수리 시간을 20% 정도 단축할 수 있고 예측 유지·보수가 가능하다. 독일 홈부르크의 보쉬 공장에서는 넥시드를 사용해 전체 물류 시스템을 최적화했다.
이를 통해 창고부터 생산 라인을 거쳐 워크 스테이션으로의 이동까지 전 과정을 투명하게 보여준다. 기존에는 재료 흐름과 상태에 대한 정보를 수집하는데 반 이상의 시간을 소비했다. 보쉬는 넥시드 프로그램이 기존 대비 효율성을 35% 높일 수 있다고 소개했다.
코로나19로 경제 전망은 비관적이지만 새로운 대안으로서의 스마트 팩토리는 나날이 발전해 나가고 있다. 이 가운데 지난 6월 초 유럽 시장을 겨냥해 독일 뮌헨에 유럽 지사를 설립한 현대로보틱스의 행보가 흥미롭다. 산업용 로봇에 특히 강점이 있는 현대로보틱스가 유럽 시장에서 어떠한 활약을 펼치느냐에 따라 코로나19 위기가 스마트 팩토리업계에서는 위기가 아닐 수 있다는 것을 방증해 줄 수도 있기 때문이다.
독일은 유럽의 로봇 전체 수요 중 약 37%를 차지할 정도로 비중이 크고 타 지역보다 로봇 수요가 압도적으로 많은 독일·이탈리아·프랑스·스페인 등 서유럽 4개국과 인접해 지리적 이점이 있다. 또한 독일 정부에서 정책적으로 디지털화와 자동화에 대해 기업에 지원을 아끼지 않기 때문에 유럽에도 특별히 의미 있는 시장이다.